This tragic event serves as a reminder of the possible risks associated with using industrial robots. It’s unsettling to consider that a machine might not be able to distinguish between a living being and an inanimate object. The victim, a worker for the robotics company, was performing routine maintenance on the robot’s sensors—a reasonably safe task. But the disastrous result of the robotic arm’s malfunction was inevitable. The incident happened in South Gyeongsang province, South Korea, at a distribution center for agricultural products.
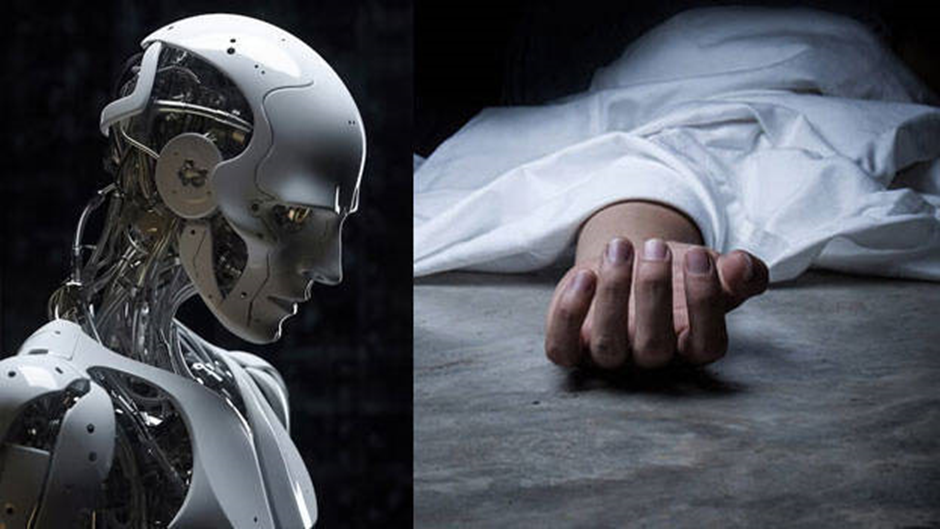
Image Source: Kerala Kaumudi
When the issue arose, the man, who was in his 40s, was examining the robot’s sensor functions. According to reports, the robot, which was made to lift and move pepper boxes, was unable to tell the difference between the vegetable crates and the man. It lifted the man as a result, and sadly, it pushed him against a conveyor belt, seriously injuring his face and chest. The man was taken to the hospital but died from his wounds.
Delayed sensor tests of robot contribute to fatal incident.
According to the background data, the employee had originally scheduled the sensor tests for November 6, but owing to reported problems with the robot’s sensor, they had to be postponed by two days. In the end, this delay played a part in the unfortunate outcome. The event highlights the need for a more comprehensive and dependable system and raises questions about industrial robot safety protocols and operational accuracy.
Following the incident, a representative for the plant’s owner, Dongseong Export Agricultural Complex, demanded the creation of a “precise and safe” system. This appeal highlights how urgent it is to address safety procedures and make sure robots have strong sensing capabilities in order to stop these kinds of mishaps.
Robot sensing has its limitations, as noted by Carnegie Mellon University robotics expert Christopher Atkeson, who emphasized that robots are not fully aware of their environment. This constraint presents difficulties, particularly in dynamic work settings where humans and machines collaborate closely. The event is a sobering reminder of how crucial it is to keep developing and enhancing robotic technology in order to improve safety features and avert catastrophic mishaps.
Robot accidents emphasize need for safety
The report also highlights a related incident that occurred in May, in which a man in South Korea was trapped by a robot while he was employed at a plant that made auto parts, resulting in serious injuries. These incidents highlight the necessity of doing a thorough evaluation of safety protocols and putting preventative measures in place to safeguard employees.
The report cites a study that highlights the historical background of industrial robot-related fatalities in the US, stating that at least 41 people died in these accidents between 1992 and 2017. It shows that 83% of fatal incidents involved stationary robots, many of which happened during maintenance tasks. This information highlights how crucial it is to put strong safety regulations into place, particularly when doing maintenance procedures, in order to reduce the possibility of industrial robot mishaps.
The sad situation involving the South Korean man is just one more in a long line of global events that highlight the possible risks connected to the growing use of robots in a variety of industries. Companies and regulatory agencies must prioritize developing and implementing strong safety protocols as technology develops in order to safeguard employees from unanticipated malfunctions and accidents involving industrial robots.